How Are Rugged Devices Tested?

20 October 2021
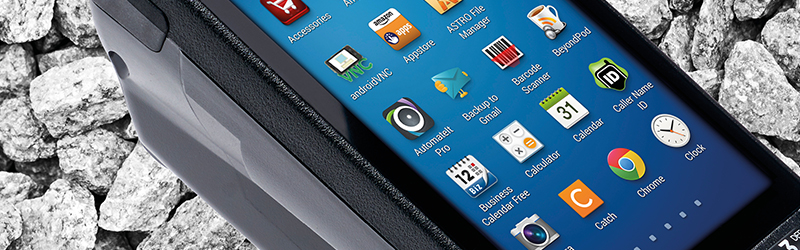
If you’re considering buying rugged devices for your
business, you want to ensure they’ll stand the test of time and do the job you
need them to do. The testing process is vigorous and is standardised across all
rugged devices. But how are rugged devices tested?
Types of rugged devices
Within rugged devices, there are three levels of ruggedness;
semi-rugged, fully-rugged and ultra-rugged. These levels show how much exposure
a device can endure which is put to the challenge during testing:
- Semi-rugged devices are enhanced versions of off
the shelf hardware meaning they share some components but are better protected.
- Fully rugged devices are designed to work in
extreme conditions and are durable, waterproof, dustproof and resistant to
drops and shocks.
- Ultra-rugged devices are created specifically
for military use which can survive the worst conditions.
Why do rugged devices need to be tested?
Product specifications are incredibly important for all
technology, but especially rugged devices. As they’re used in the most demanding
and potentially hazardous situations, rugged hardware needs to be resilient to
drops, water, dust and shocks. They need to be reliable and not break after the
first knock or drop.
For many businesses, rugged devices are an incredibly
important part of the supply chain and need to be relied upon for the continual
flow of information and data. Any downtime caused by a malfunction or broken
device could cause financial losses due to the disruption to the manufacturing
process or supply chain. Therefore, it's incredibly important that rugged
devices are tested to ensure their level of ruggedness is what the company
needs, and has paid for.
How are rugged devices tested?
Although rugged devices are all created to minimum industry
standards, they are not built the same and must be tested to demonstrate their
durability. Can your chosen device withstand an accidental drop from a
forklift, or being left in a cold environment by accident?
Given the demand on devices, they are tested and measured in
two ways; IP Rating and MIL-STD-810.
IP Ratings
IP Ratings are a common set of testing standards used in the
UK. Developed by the European Committee for Electro Technical Standardization
(CENELEC), IP Ratings, also known as Ingress Protection, provides a standard to
define the levels of sealing effectiveness of an electrical device. The sealings
need to be able to protect the device from foreign materials including water,
dust and dirt which could damage the internal components.
To conduct the IP rating tests, third party laboratories and
specialist equipment is used to ensure each test is conducted in the same way. The
equipment includes immersion tanks, water, dust nozzles and jets.
What do IP Ratings show?
IP Ratings are shown by IP followed by two numbers which
correspond to solid ingress and liquid ingress.
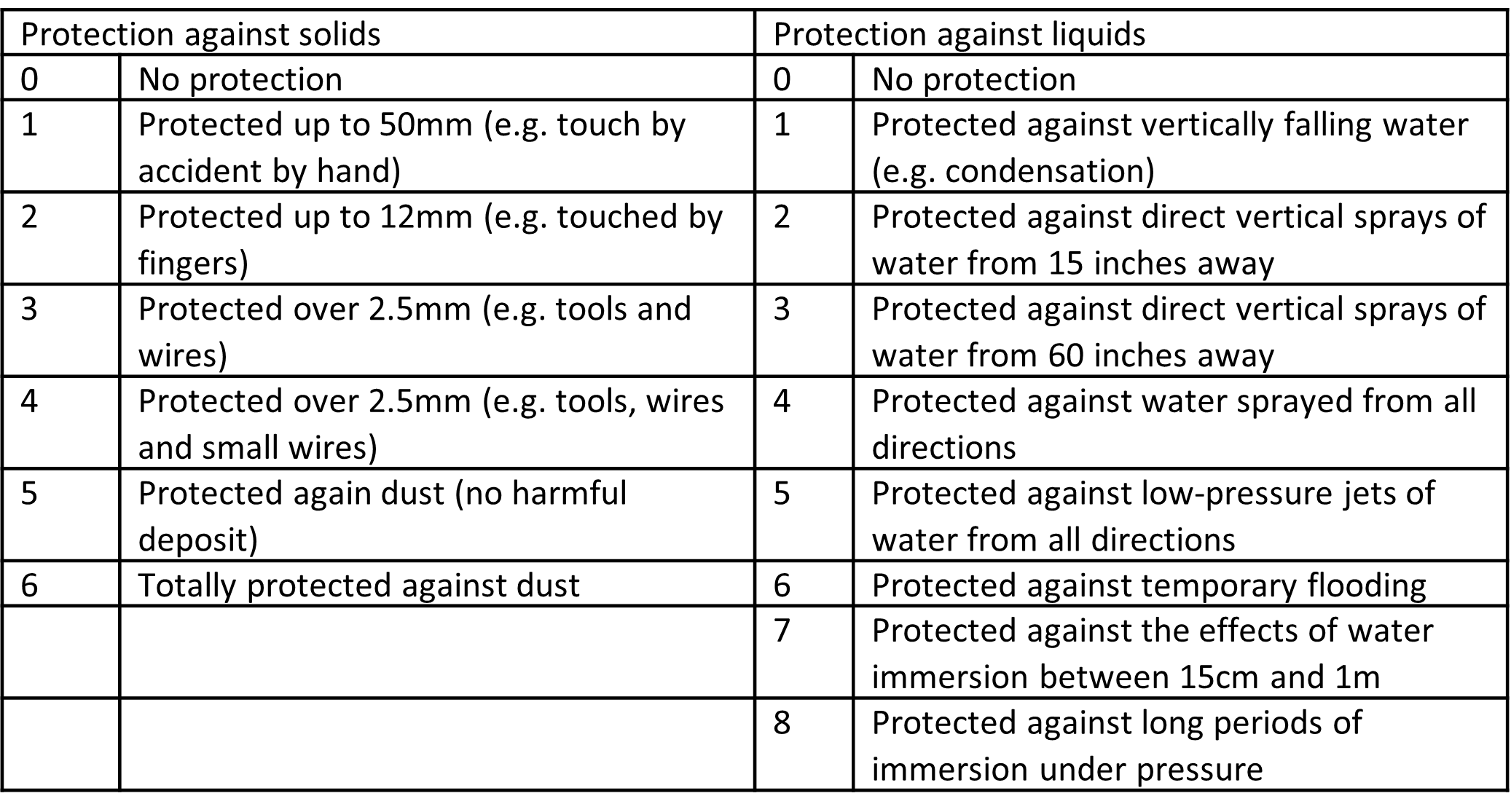
For devices to be considered as fully-rugged, they must
achieve a minimum rating of IP54 which means the device is protected against
dust and has some water resistance. At TouchStar, devices such as the handheld TS8200
and vehicle mount TS3200 have
a rating of IP54.
In industries where higher levels of protection are needed
such as manufacturing or hazardous environments, an IP rating of IP65 or higher
is recommended. This means a device can completely withstand dust, dirt and low-pressure
water, and can also withstand a meter drop.
In construction, an IP rating of IP67 or higher would be
preferable as this would ensure they could withstand a one-meter water submersion
for up to 30 minutes. At TouchStar, our handheld TS5000
device has a rating of IP67.
MIL-STD-810
To conform to MIL-STD-810 standards, devices have to endure
a series of tests created by the US Military. The 29 tests assess how the
technology performs at an optimal level under harsh environments, and are
extremely extensive by covering a range of situations and conditions. They’re
conducted in laboratory conditions and cover changing weather conditions,
pressure changes, drops, shocks, and heavy vibrations.
The MIL-STD-810 standards are often revisited, updated to
reflect changes in technology and demands. In January 2019, the newest
standards were letter H which made some significant changes to the previous
version G. These amends were made to multiple sections including the Test and
Evaluation Master Plan (TEMP), procedures for high temperature testing and
procedural changes to immersion testing.
As this level of testing is not required in the UK, not all
rugged devices are tested against the MIL-STD-810 standards. Therefore it’s
worth checking the specification of any rugged device you’re considering if you
require it to meet US military standards.
Find out more
Here at TouchStar, we offer a range of rugged devices which
has been thoroughly tested to ensure they’re suitable in many different
environments and sectors including logistics and manufacturing. To find out how
they could benefit your business, get in touch today.
ABOUT THE AUTHOR - PETER MARSH
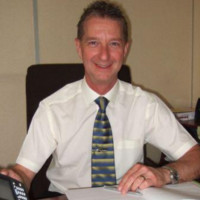
Peter joined TouchStar (formally Belgravium) in a sales manager role in 2001. Prior to joining the company, Peter held Partner and National Sales Manager roles within the parcel and logistics industries.
In 2011 Peter was promoted to Sales Director and is now actively involved in promoting the value of TouchStar’s Rugged Mobile Computing solutions to the warehouse, logistics, manufacturing and field service industries. When not involved in the business, Peter is a keen and enthusiastic football and cricket fan.