TouchStar State of the Nation 2019: Technology trends in the warehouse

19 August 2019
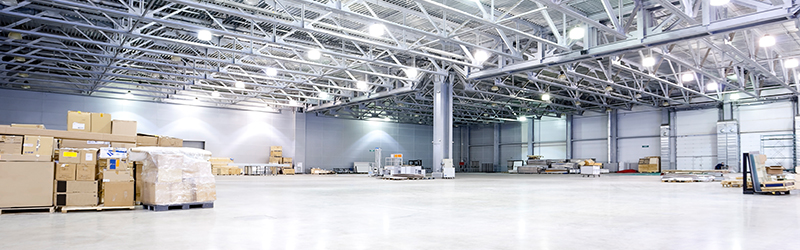
The key goals of implementing new
technology in a warehouse environment have traditionally fallen into two camps:
increasing staff productivity and replacing inefficient (often paper-based)
processes.
But now more than ever before,
warehouses are having to adapt at a blistering pace to keep touch with high
customer expectations, staff shortages and the impact of Brexit. TouchStar’s
Peter Marsh assesses the current technology landscape and looks at how new
advancements can help warehouses over the next year and beyond.
What is
driving the implementation of new technology in the warehouse, and what
challenges are standing in the way?
PM: A lot of people are looking at
automation, but it’s a very expensive model to pursue. That’s why we have only
seen the biggest companies bite the bullet and drive forward with automation.
Many of these businesses would have been very manual labour-led and bringing in
automation has delivered significant efficiencies for them.
Taking a
step back however, and the real drive behind most new implementations of
technology is the need for real-time data. Recent research has shown that
boosting productivity and efficiency is at the top of most warehouse managers’
wish lists, and while that isn’t at all surprising, what is interesting is that
they are achieving their goals by being smarter about collecting and reviewing
data.
For many
warehouses, the speed at which data can be collected and the ability for that
data to be analysed and acted on is vital. Technology that helps to bridge that
gap is in demand. It’s not just about replacing paper-based processes any more.
Every action in the warehouse can give insight on how to improve the operation
as a whole, and the right technology can make all the difference.
How are
warehouses coping with new demands, faster requirements and other modern-day
issues?
PM: What we have seen in the last few years
is that pioneering services offered by companies like Amazon have changed the
game. They’ve radically changed the public’s perspective of warehouses, and
they’ve given managers cause to consider how their warehouses should be set up
and operate.
Of course,
the traditional issues like capacity, workforce and order volume are still
there. But now there are new requirements that customers suddenly take for
granted, like rapid returns management.
While customer
perspectives can change rapidly, warehouse procedures can sometimes take longer
to adopt new practices. But we are seeing advancements and strategies designed
with new customer demands in mind.
Again,
central to this is real-time data. If you have the visibility to know an order
status and see where items are in real-time, and you keep the customer updated,
you tick many of the boxes of a what is expected in a modern warehouse.
Using a
business like Amazon as a benchmark is useful, but we always have to bear in
mind the financial muscle it has to solve any problems or invest in brand new
technology on a regular basis. But the model can be scaled-down and made
effective in smaller, mid-tier warehouses. It’s about being clever with your
budget and picking the areas where technology can have the biggest impact.
How has
Brexit affected investment in new technology?
PM: It’s very much a double-edged sword.
Some companies are seeing more business than ever before due to stockpiling.
Many will have to manage that stock all over the country, moving it or finding
locations to expand.
But there
is also a lot of uncertainty. Businesses that may have operated on a three- to
five-year cycle when it comes to technology are instead looking to squeeze the
value from their current set up and move to a five- to seven-year cycle
instead. It’s not fully down to Brexit, but it’s certainly given boards cause
for concern.
Most
general warehouses are being clever about the way they spend their money. There
are no guarantees about what will happen on October 31st – or later.
So if equipment is working, is effective, is still supported, then the
pragmatic choice is to wait perhaps another year and assess the situation then.
For others
it will depend on their specific needs. Those relying on five-year-old tech or
older will find that new demands could overwhelm them, especially the
requirement for real-time data as we’ve already discussed. It’s a decision that
will need to be made; the question is whether it will be made now.
The
winners in this time of uncertainty will be the ones that make positive
decisions. Delaying decisions and waiting may appear the safer play, but
ultimately it risks falling behind. Relying on outdated technology is a
sure-fire way to encounter problems, so it’s better to get ahead of the pack
now.
What new
technologies have been most successful in the warehouse over the last 12 months?
PM: This year it has been more about
operating systems that have driven change in the warehouse, predominantly the
move from Windows to Android.
There’s
technology that often gets tagged as ‘new’ like voice or wearables, but the
truth is that they have been around for a number of years but usually operate
in the background. Many deployments that initially focus on voice or wearables
have quickly run into issues, like jackets that make it difficult to use
wearable tech, and businesses eventually move to more traditional systems.
Although
the next ‘big thing’ is tempting, the best piece of advice I can give is to concentrate
on what will work for your specific operation – and usually that means a simple
but flexible solution.
The
warehouse manager’s role has changed dramatically over the last 15 years, and a
crucial part of it is selecting the right technology, often with the help of a
trusted advisor. But there’s a reason why traditional scanning technology is
still in demand: it’s effective, efficient and easy to use.
Is full
automation in the warehouse a risk? And if so, what are the best ways to
implement partial automation?
PM: It is a risk and unfortunately we have
seen examples where large scale automation has not paid off. In some cases, it
has been less efficient than the previous solution.
But others
find it works very well. Of course, automation isn’t anything new and there
have been many successful deployments over the years. But you do have to
consider all outcomes carefully, which is why some prefer a more partial
implementation.
For
example, rather than expecting automation to replace staff many warehouses actually
use automation to enhance their staff, making them more productive and removing
a lot of repetitive work and data collection to save time, money and energy.
ABOUT PETER MARSH - SALES DIRECTOR, TOUCHSTAR RUGGED MOBILE COMPUTERS
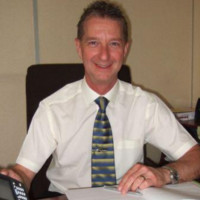
Peter joined TouchStar (formally Belgravium) in a sales manager role in 2001. Prior to joining the company, Peter held Partner and National Sales Manager roles within the parcel and logistics industries.
In 2011 Peter was promoted to Sales Director and is now actively involved in promoting the value of TouchStar’s Rugged Mobile Computing solutions to the warehouse, logistics, manufacturing and field service industries. When not involved in the business, Peter is a keen and enthusiastic football and cricket fan.