Expect Distribution Case Study: Warehousing and Palletised Distribution

24 March 2021
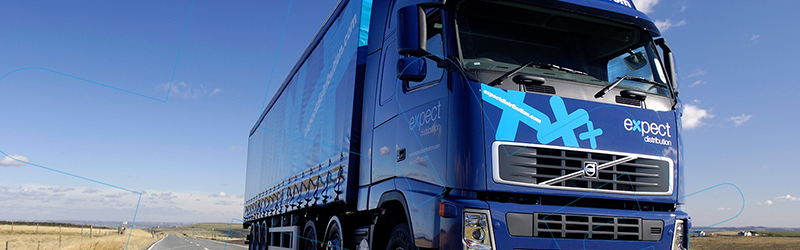
From
palletised and international distribution, through to contract logistics and
warehousing, Expect Distribution have built long term partnerships with their
clients, delivering real competitive advantage through the provision of
reliable, flexible and profitable logistics operations.
A multi
award winning company, Expect are widely acknowledged as market leaders,
adapting and investing in their operations to meet the needs of the logistics
industry all over the UK.
With over 250,000 sq ft of warehouse space across the North
of England, Expect provide both shared user or fully managed 3PL solutions, offering
specialist and bespoke services that deliver real cost benefits to their end
users.
Challenges
Expect are continually investing in their IT infrastructure.
A planned growth within their Bradford operations resulted in a decision to review
additional RF scanning requirements. RF scanning plays a key role in supporting
Expect’s IT infrastructure, providing real-time stock level updates in addition
to supporting
pick accuracy and operational efficiencies.
Expect were looking to implement a future proof and scalable
system to support their goods in and picking operations. Expect turned to UK
based rugged mobile computer and scanning specialists, TouchStar Technologies, to
manage the process from specification through to testing, go live and ongoing
support.
The rugged
devices would need to use information from Expect’s core warehouse management
system (WMS) to confirm receipt of palletised goods and what stock items to pick
for goods out. To facilitate the real time data capture, TouchStar needed to
ensure full connectivity with Expect’s new Wi-Fi network.
Solution
At the core of the system is TouchStar’s TS8000 series handheld rugged
mobile computer. The TS8000 offered several advantages for the users on site. With its optimally positioned hard capped keys,
the TS8000 was the perfect device for Expect’s scan intensive warehouse
operation. Not only that, the availability of a hot swappable battery,
guaranteed continuous operation and reduced downtime, maximising output, and
increasing workload efficiency.
Implementation
The go live
of the RF system was to coincide with a new contract that had been awarded to their
new Bradford warehouse operation. Expect undertook a thorough five week testing
period, checking compatibility with their core warehouse management system and
connectivity with the Wi-Fi network. TouchStar engineers were on hand
throughout, ensuring the correct configuration and set up of the new scanning devices.
Outcome
The support
of TouchStar prior to the system going live resulted in a smooth deployment. Benefiting
from a UK supported solution, Expect have experienced minimal downtime. The
devices have met the scope for the project, providing advanced scanning
capability and real time visibility.
Chris Ramsden, Warehouse
Operations and Systems Manager, comments, “The implementation was very
successful, TouchStar had a wide range of technical knowledge and experience
and have been invaluable in their support during the testing phase and go live.
The user feedback on the devices has been great, they are both ergonomic
and easy to use, perfect for our scan intensive environments.”
Since the initial deployment, the devices have been rolled out
across two of their North West sites. As a scalable and proven solution, Expect are now
looking at additional scanning options to support their peak period. TouchStar
has continued to provide guidance to help Expect define the requirements.
Chris
continues, “Since we went live TouchStar has always been there to assist with
any questions or changes we have had to the systems we have put in place. We
look forward to working closely with TouchStar on our future planned projects.”