Lakeland Case Study - Streamlining Efficient Retail Operations With Rugged Mobile Computers

17 January 2022
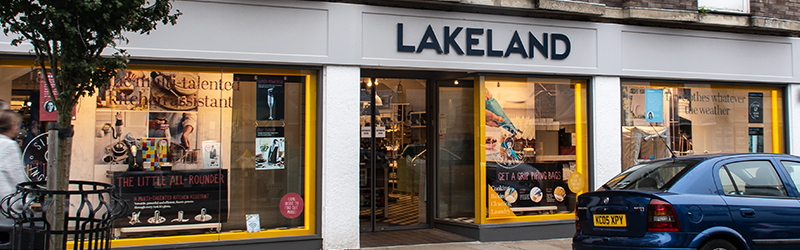
As one of the UK's home
shopping pioneers, Lakeland is one of the
leading names in kitchenware and home ware products.
Founded by Alan Rayner
in the 1960’s, Lakeland have grown to become one of the UK’s most respected
family run retail businesses. From selling freezer bags at the farm gate in the
1960’s to managing a growing number of retail outlets, their success has
continued with a rapid growth in online sales as they help customers make the
most of their time at home.
The Role of RF
Lakeland attributes the ongoing success
of the company to following the simple philosophy, “always look after the
customer and the business will look after itself”. Indeed, Lakeland remain
extremely customer orientated and pride themselves on setting themselves apart
from the rest with their friendly, speedy, personalised service and modern,
welcoming retail stores.
The optimised running of their Kendal
distribution centre has been fundamental in maintaining this philosophy. The
installation of their first RF system in 1996 enabled real time visibility of
their warehouse, their stock levels, and processes. The technology had been
implemented within various departments throughout their general
warehousing/picking operation, helping them to optimise the many processes such
as put away, picking and replenishment.
As the business continued to grow,
further upgrades were made to the system to ensure they continued to operate
effectively with minimal error and cost to the organisation.
Maintaining High Standards
Since the initial system was installed, the
Kendal based warehouse operation now manages the distribution for over 60 stores
nationwide as well as fulfilling customer orders placed through their website
and over the phone. In recent years,
Lakeland have seen significant growth in the e-commerce sector and combined
with their mail order business, they now distribute thousands of parcels a day
via their direct despatch operation.
Lakeland fully understands and appreciate
the effectiveness of their RF system and like to source the most up to date
systems and radio data terminals. Commenting on the effectiveness of the system
Alex Rea, Systems Manager for Lakeland says, “The benefit of the system means
that we always have real-time information to hand on every facet of the
operation such as allocated tasks and stock location. All this information
helps provide our customer with a speedy and responsive service which is
critical in ensuring our customers have a great shopping experience.”
Facing an even faster turnaround and the continued
challenge of maintaining reliable, streamlined operations, Lakeland once more turned
to TouchStar Technologies for a mobile computing solution.
The Solution
The new project extends the successful
relationship with TouchStar which now spans over 15 years.
Alex continues, “Touchstar devices had
proved themselves inherently reliable within our operating environment, over a
significant number of years. We know TouchStar install quality systems so,
recognising it was time for a hardware refresh, it made sense to start talking
to them about how we could move on to a future proof system”.
Working together with TouchStar to select
the best solution for their warehouse, Lakeland selected TS7200 truck mounted
terminals. The devices combine high impact polycarbonate plastics, metal alloy
chassis and the use of Sorbothane® rubber shock absorbers to provide an
extremely reliable solution and prolonged life within Lakelands robust
warehouse environment.
With high-definition graphics and
keyboard the TS7200 also provided outstanding readability. The integration of a fully capacitive QWERTY keyboard also meant that
Lakeland benefited from an easy to use, robust wipeable touchscreen with its
large keys perfect for their data entry applications.
Ongoing Success
As Lakeland continue to grow, the upgrade
has provided Lakeland with the confidence that they are able to maintain the
high service levels that they are renowned for. Alex continues, “The new
hardware has enabled us to maintain efficient warehouse processes. The
availability of accurate real time stock movement updates means we have 100%
confidence that all stock information is right up to date. With TouchStar we
have enjoyed excellent local support, so downtime is minimal, and our
operations are more cost effective”.
Lakeland is excited by the potential that
radio frequency technology offers about further process improvements. This
potential has already been fully realised in key areas of the business and
continues to help Lakeland deliver unsurpassable customer service levels and
secure tangible operational improvements.